Customized Aerospace & Defense
Molded Cable Assemblies
Molded cable assemblies provide a multitude of benefits, such as water resistance, abrasion protection, and highly effective strain relief. By reducing flex-induced stress on wires, connectors, and contacts, these assemblies ensure optimal performance and longevity..
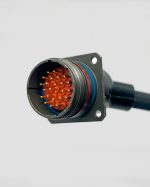
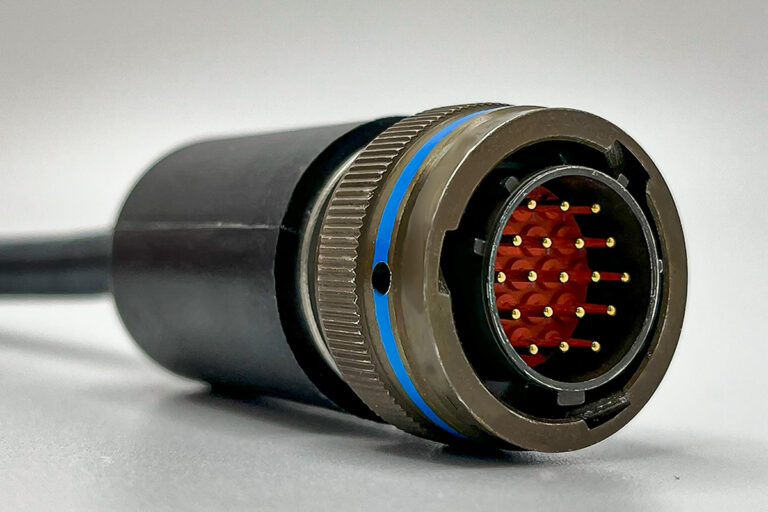
Explore the resilience of Nortech’s molded cable assemblies. Boasting strain relief and industrial-grade sealing, these assemblies offer superior water-resistance, shock absorption, and abrasion resistance. The advanced casting method ensures a lasting watertight seal. Tailored to fit in even narrow spaces, Nortech’s assemblies utilise various tested, robust materials. Experience the mix of reliability, performance and affordability that Nortech delivers in cable solutions.
Advantages of Molded Cable Assemblies
Molded cable assemblies offer numerous advantages including water-resistance, abrasion protection, and maximum strain relief effectiveness. Flex-induced stress on wires, connectors, and contacts is significantly reduced. The molding process provides excellent electrical insulation properties, less exposed metal than mechanical backshells, and the cable can enter the connector from any angle, providing ample flexibility. Nortech has the capabilities to cast various materials, including urethanes, silicones, and epoxies. We can also transfer mold elastomers, i.e., Neoprene and fluorocarbon elastomer, and injection molding of thermoplastics, i.e., polyurethane, and PVC.
Cables with molded connector strain reliefs and junctions provide superior reliability to shrinkable boots and mechanical backshells. Molded assemblies are sealed for life and provide excellent strain relief, environmental protection, abrasion protection, shock and impact resistance, most often at lower cost.
Benefits include:
- ability to custom fit into tight spaces
- allow cables to exit connectors at any angle
- excellent aesthetics
- Moldings do not utilize shrink boot adhesives that break apart in the cold or with age.
- Cables with moldings do not pullout due to cold flow as can happen in a cable clamp or grommet.
Construction of Molded Cable Assemblies
-
2-Part Cast Molded Cables
-
Rubber Transfer Molded Cables
-
Injection Molded Cables
Advantages
Moldings created with a cast 2-part molding process provide excellent sealing properties as the materials used chemically bond to the backshells and cable jackets. These materials are chemically cured materials and will not melt or deform with temperature. They have superior low and high temperature capability and environmental resistance compared to thermoplastics. These materials can be economically used in very low quantities and can scale up to high quantities using inexpensive tooling. These materials are cured at elevated temperature to speed the curing process.
Typical Materials
Polyurethane. Polyurethane is a tough flexible material with excellent sealing and strain relief properties. It can be used with thermoplastic polyurethane and neoprene jackets. It has been used for decades as an industry standard. The most often used specification is MIL-M-24041 Category B Type 1. Nortech utilizes multiple automated dispense machines to fill molds with this material.
Silicone. Silicone is highly flexible material with a wide temperature range. It should be used with compatible silicone jackets or silicone molded flat cable. It is not as durable as polyurethane. Typical material callout is Dow Corning Sylgard® 186.
Epoxy. Epoxy is more often used for potting applications than overmolding. Epoxy is typically hard with little flexibility. Typical material callout is Henkel Stycast 2651/CAT 11.
Cast Mold Tooling
Nortech has been producing cast molded assemblies since 1964 and has a large inventory of mold tooling. The mold tooling uses interchangeable parts to allow different connectors and cable sizes in the same mold body. For standard straight or right angle molds, we will most likely have tooling available for immediate use. Because this tooling is not complex, and is made of aluminum or 3D printed, lead times and cost to produce custom tooling is minimal.
Advantages
Moldings created with rubber (elastomer) transfer molding provide special advantages over cast molding depending on the rubber material. The materials used are uncured rubber which is pushed into the mold and cure with pressure, temperature, and time. Rubber molded cables should be molded to like rubber jackets (e.g. EPDM to EPDM).
Typical Materials
Polycholoroprene (Neoprene) per MIL-PRF-6855, Class 2, Type A, Grade 60, Fungal Resistant. Low temperature flexibility, general purpose.
Ethylene Propylene Diene Monomer (EPDM) per ASTM D 2000 M2DA607,Fungal Resistant. Low temperature flexibility, weatherability-UV resistance-water resistance.
Fluorocarbon Elastomer (Viton®) per ASTM D 2000 M3HK607A1-10B37C12EF31 or AMS 3216. High temperature resistant, Fuel-Hydrocarbon resistant.
Transfer Mold Tooling
Transfer mold tooling is made of aluminum except high volume runs are made from steel. It is non-complex and inexpensive to design and manufacture custom tooling. Existing tooling is available for many circular connectors.
Advantages
Moldings created with thermoplastics provide superior aesthetics and can be molded with intricate detail and surface texturing. Using primers, thermoplastics can be bonded to other thermoplastics and metals. Injection molding is well suited to high volume production runs.
Typical Materials
Thermoplastic Polyurethane. Thermoplastic polyurethane is a rugged flexible material with good low temperature properties. It can be provided in low smoke non-halogen grades. Typical materials used are Lubrizol Estane® 58300, 58202, and 58370.
Santoprene™. Santoprene thermoplastic vulcanizates are thermoplastic elastomers with excellent flexibility. Typical material used is Santoprene 101-55.
Injection Mold Tooling
Injection mold tooling is available for many D-Sub connectors and circular connectors. Typically, aluminum is used for medium volume tooling at moderate cost. For low volume runs up to 100 pieces, Nortech offers 3D printed mold tooling for low cost and quick turn production or prototype assemblies. High volume steel tooling with inserts and texturing is higher cost.