In today’s fast-paced manufacturing landscape, front-line manufacturing workers will benefit from digital tools to streamline their operations which create an advanced manufacturing environment, furthering the elevation of production and performance to new heights.
The Digital Diagnostics Maintenance Interface is a paradigm shift in performance optimization. By supplying real-time monitoring capabilities and proactive maintenance alerts, this innovative interface ensures enhanced reliability and seamless operation. Originally born from the telecommunications sector’s relentless pursuit of efficiency, DDMI has transcended industries like manufacturing, healthcare, energy, and telecommunications to deliver unparalleled diagnostic insights driving operational excellence.
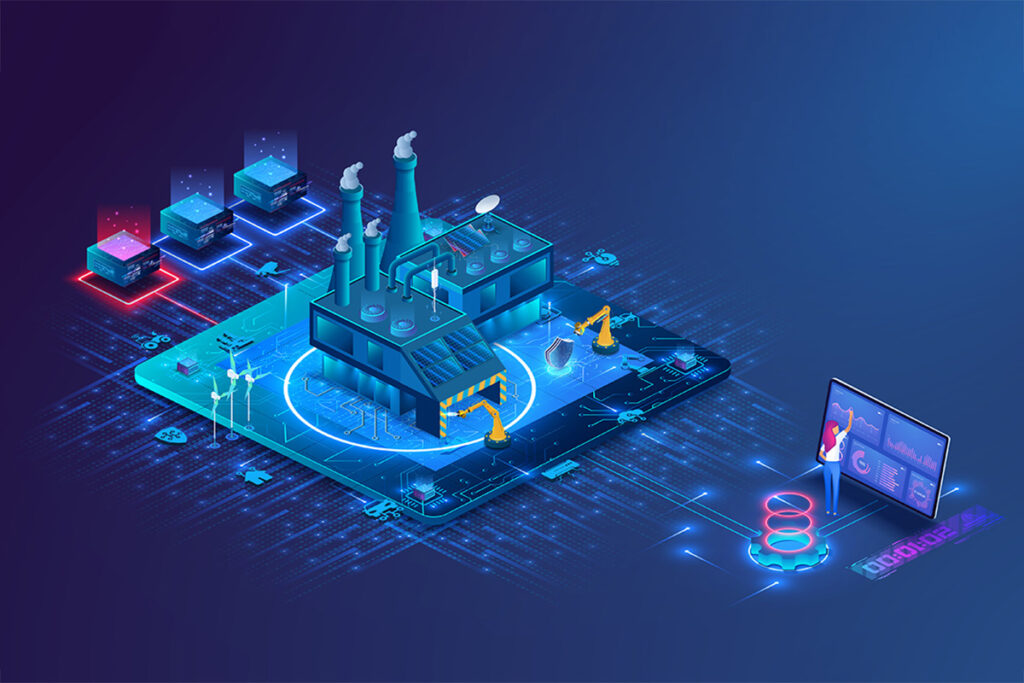
According to the Manufacturing Leadership Journal, a staggering 79% of manufacturers still rely on manual paper-based instructions and progress tracking, resulting in lost productivity opportunities. Embracing DDMI can revolutionize manufacturing plants by empowering employees through high-precision sensors and sophisticated software algorithms. From meticulously monitoring minute fluctuations to navigating vast data landscapes, DDMI seamlessly integrates into the production system fabric without disrupting workflow – ushering in an era of unobtrusive value.
DDMI practices can offer significant benefits for manufacturers across various aspects
Minimize downtime:
These advanced manufacturing practices can use sensor data and historical information to diagnose potential equipment failures before they occur. This allows for timely repairs and replacements, preventing incidents- and minimizing downtime.
Increased efficiency:
By optimizing maintenance schedules and reducing downtime, employees can focus on more productive tasks. Predictive analytics allows manufacturers to predict potential pain points. Identifying early warning signs enables manufacturers to proactively replace, repair, and maintain their equipment before production hindrances.
Data-driven decision-making:
Access to data and insights can empower employees to take ownership of their tasks and make informed decisions. Advanced manufacturing through DDMI empowers decision-making by using historical equipment data. Manufacturing employees can make informed decisions about equipment purchases, maintenance schedules, and resource allocation.
ESG Benefits:
DDMI can determine and optimize energy usage, leading to a lower carbon footprint and improved energy efficiency. By preventing equipment failures and optimizing production processes, DDMI can help reduce waste generation and resource consumption. Implementing this advanced manufacturing interface demonstrates a commitment to sustainable manufacturing practices, which can enhance brand reputation and attract environmentally conscious customers.
Implementing DDMI requires investment in technology, training, and data analysis capabilities. Successful diagnostic interfaces require a cultural shift towards data-driven decision-making and collaboration between different departments.
Stepping Into the Future of Advanced Manufacturing
As technology continues to evolve, manufacturing practices and tools should continue to improve. Manufacturers have the responsibility of keeping up with an innovation that will improve their processes and deliverables. Overall, embracing DDMI can offer significant benefits for manufacturers. By leveraging data effectively, manufacturers can create a more efficient and sustainable work environment.