Do you know what molded cable assemblies are? These cables are used mainly for ruggedized aerospace and defense applications. We are proud to produce this critical technology at our Blue Earth facility in southern Minnesota. At Nortech, we understand the need for reliability and sensibility in molded cable design, and we are here to help. Nortech provides the vital protection your products need to keep performing at the highest levels.
The molded cable construction process carefully selects materials, tooling types, and assembly techniques to assure top protection. Molded cable assemblies provide many advantages for reliability and cost reduction.
How Nortech's Molded Cables Protect Your Technology
Molded assemblies offer many benefits: Superior water resistance, abrasion protection, strain-relief effectiveness, customizable fits for tight spaces with the ability to exit and enter connectors at any angle, and exceptional aesthetics. The outer molding provides additional pull strength and prevents damage at flex points. Additionally, molded cables do not pull out or break apart when in contact with the cold or during the aging process. Because of this, your replacement needs and costs will go down. These assemblies are sealed for life which saves you time and money.
Our dedicated employees provide product excellence from start to finish and every step in between. Nortech provides multiple ways to create molded cable assemblies, each with their own benefits. We understand this process can seem intimidating, but we are here to help every step of the way.
Contact us today to get started on your next project.
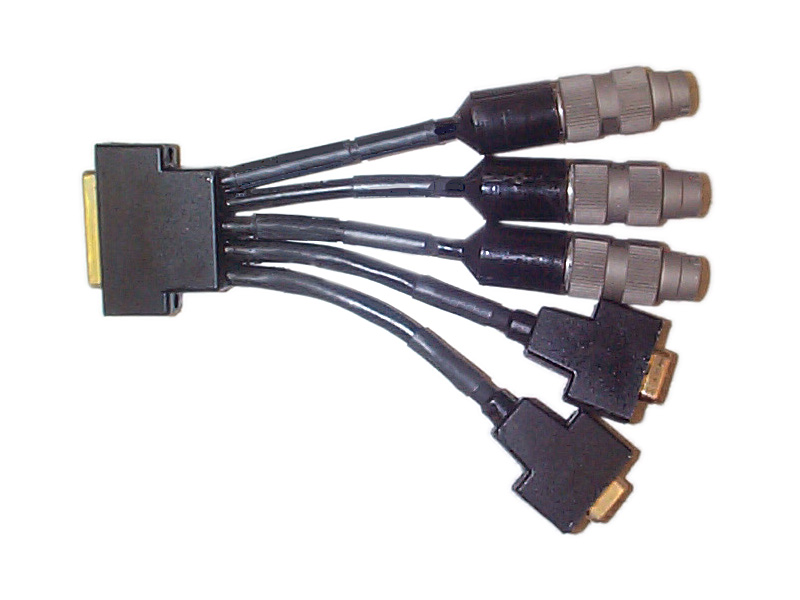
3 Critical Components of Molded Cable Assemblies
1. The casted two-part process provides impressive sealing properties because the materials chemically bond to the backshells and cable jackets. These materials are chemically cured and will not melt or deform with temperature. All of these materials can be economically used in low quantities and can scale up to high amounts using inexpensive tooling. The typical materials used include polyurethane, silicone and epoxy.
2. Rubber (elastomer) transfer molding provides extra dependability. It uses uncured rubber, which is pushed into the mold and cured with pressure, temperature and time. Rubber cables are designed to be molded into rubber jackets (e.g., EPDM to EPDM). The common materials used include polychloroprene, ethylene, and propylene diene monomer.
3. Injection-molded cables using thermoplastics provide injection molded cables. This helps enhance the aesthetics, including superior detailing and surface texturing. With the use of primers, thermoplastics can be bonded to other thermoplastics and metals. Injection molding is ideal for high volume production run rates. Commonly used materials include thermoplastic polyurethane and santopren.
Why Choose Nortech?
We offer two methods to tool for molded cable assemblies. In most cases, we use traditional metallic-based tools, which would be aluminum and steel for high volume designs. These tools are simple to design and inexpensive to manufacture.
At Nortech, we’re proud of the products we make and our ability to support some of the world’s most advanced and demanding applications. From stealth fighters to tactical communication systems, we are ready to help. Our continued attention to detail from beginning to end makes Nortech Systems one of America’s most respected and trusted cable manufacturers. Our product quality is unsurpassed, and we maintain a quality system that meets ISO-9001 and AS-9100 requirements.
We will meet any of your production or specification needs. Just as important, our customer service is involved in each step of the manufacturing process, ensuring we will be there to answer any questions you have. We thrive on helping our customers succeed.
Contact us to start your molded cable assembly project now!