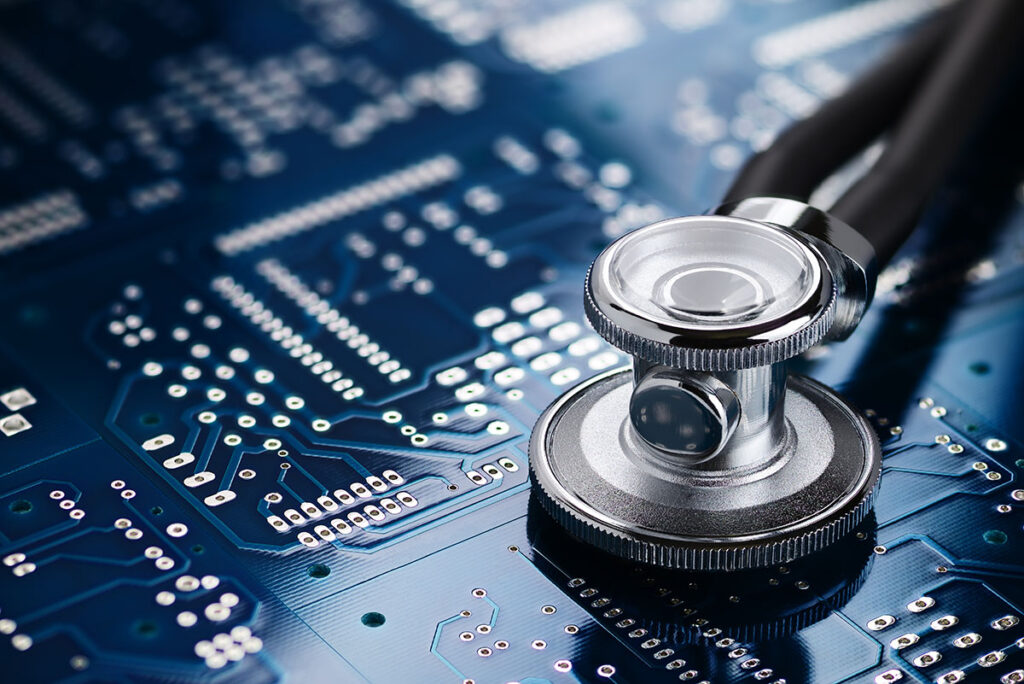
Medical professionals rely on state-of-the-art technology including PCB boards designed specifically for medical devices. Medical devices are designed to offer precision, reduced weight, cost-effectiveness, and flexibility. Given the critical nature of medical procedures, it is imperative that all healthcare equipment be rugged and durable, and able to withstand the environmental demands of a busy healthcare setting. To ensure optimal care, crucial medical devices like defibrillators, heart monitors, and other healthcare tools require detailed planning, development, and the latest technology. Since the lives of patients depend on the efficacy of medical devices and the efficiency of hospital practices, maintaining high standards of reliability necessitates meticulous attention to detail and top-tier quality in the design and manufacturing of PCB boards specifically tailored for medical devices.
PCB boards (printed circuit board assemblies) play a critical role in numerous medical devices. As the number of wireless devices increases, medical professionals need the capability to transmit and receive greater information and large data seamlessly. Healthcare providers rely on medical devices to deliver the best care. Devices used by medical professionals must exhibit resilience to harsh environmental conditions, including extreme temperatures, vibration, and radiation. Furthermore, they must adhere to stringent safety standards, given their potential use in life-critical applications. Including custom designed PCB boards in their medical device design, manufacturers can ensure that their medical clients are equipped with effective and reliable devices, contributing to improved patient care and outcomes.
Select a Partner with Deep Medical Device Expertise
Selecting a manufacturing partner with deep medical device expertise will ensure your custom PCB board design meets your project requirements. By carefully considering the unique needs of the medical industry, PCBA manufacturers can develop solutions to meet the highest standards of safety, reliability, and performance. This will help to ensure patients receive the best possible care as medical devices continue to play a vital role in improving health outcomes.
Adhere to Industry Standards
As a result, it is important to follow best practices when prototyping and testing PCBAs for medical applications. Here are some key considerations quality EMS providers should make:
- Quality Standards: Ensure that the PCBAs meet the standards of the medical industry, such as ISO 13485. These standards are important because they ensure the safety and quality of the products. They cover a wide range of requirements including:
- Design control
- Risk management
- Process validation
- Inspection and testing
- Control of nonconforming products
- Document control
- Corrective and preventive action
- Management review
- Reliability: PCB boards must be highly reliable and perform consistently over time. Components and materials should be selected for their durability and long-term stability.
- Component Selection: Use medical-grade components with extended temperature ranges, high accuracy, and low failure rates to ensure the reliability of the PCB boards.
- Testing Protocols: Develop comprehensive testing protocols that cover functional, electrical, and environmental tests to ensure the PCBA’s performance and safety.
- Safety: Implement fail-safe mechanisms, isolation barriers, and proper grounding to prevent any potential harm to patients or operators.
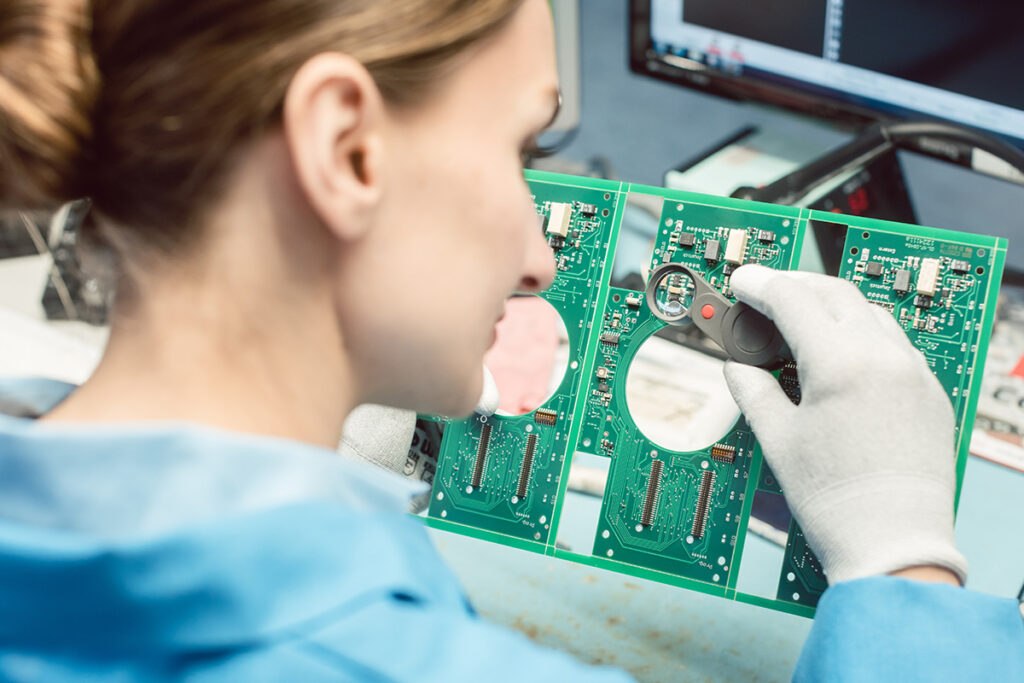
Other Important Considerations for PCB Boards
In addition to the points mentioned above, here are some other important considerations for PCBAs in medical devices:
- The use of miniaturized PCBAs is becoming increasingly common in medical devices, as it allows for smaller and more portable devices. However, miniaturization can also pose challenges, such as increased complexity and the need for more precise manufacturing techniques.
- The use of flexible PCBAs is also growing in the medical industry, as it allows for devices that can be bent or folded without damaging the PCBA. This is particularly useful for wearable devices and implants.
As the medical device industry continues to evolve, PCBAs will play an increasingly important role in the development of new and innovative technologies. By staying up to date on the latest trends and developments, PCBA manufacturers can help to ensure that their customers have access to the best possible products.
Nortech System Inc. is a global manufacturing partner for custom and complex manufacturing solutions. We engineer ruggedized PCB boards to withstand even the harshest environments, promising dependable performance. With integrated capabilities in testing, prototyping, and design all under one roof, we deliver quality products on time. From rigid or flexible form factors to complex geometries and miniaturization, Nortech excels highly customized, low volume production. Our engineering and manufacturing teams ensure designs are ready for production. Our facilities are ISO 9001-2008 and ISO 13485-2003 certified, ensuring the highest quality standards are met.