Questions to Consider:
Are your complex electro-mechanical devices causing inefficiency and costing more money to manufacture? Or is communication and product lifecycle management causing delays in manufacturing? That is what a Nortech client was experiencing when they first brought their unique medical device to the table.
Our client, a well-known surgical and medical device company, recently came to us with a product development issue. They needed our help taking a custom-made Bluetooth console and multiple probe models from a two-piece board assembly to a one-piece board, making it much more efficient to build. The challenge was maintaining the same level of functionality that identified and removed cancer in the body while trying to minimize assembly parts and increase manufacturing efficiency and increase manufacturing yield.
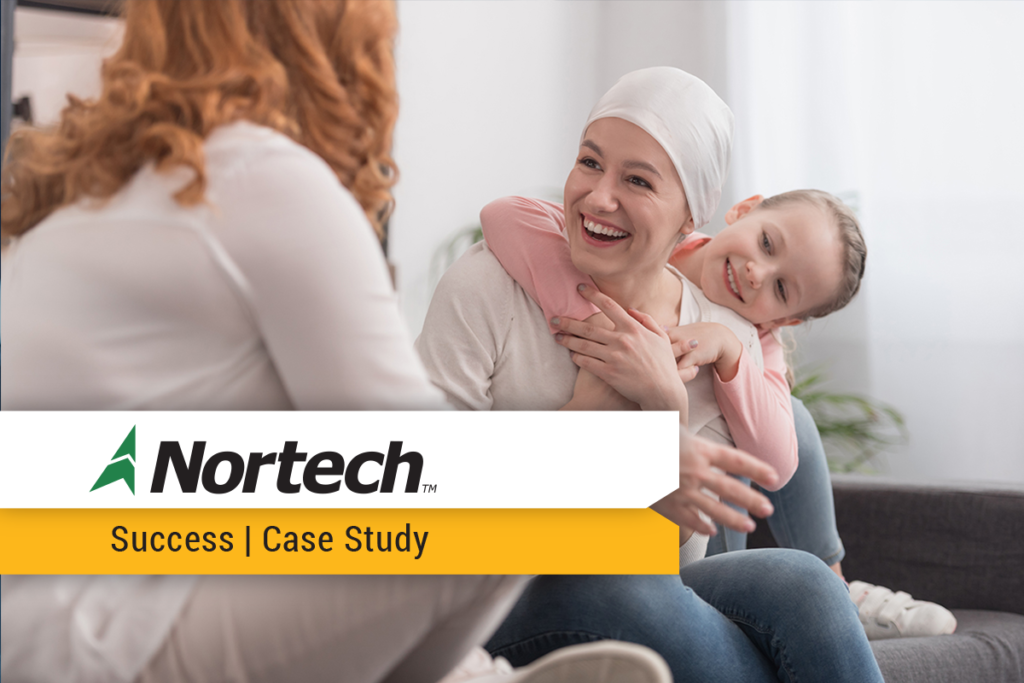
The multiple probe models working in concert with the console are used to identify in the body areas of concentration of the drug given to the patient. This probe detected concentration of the drug can indicate cancerous tissues. Those tissues are removed and biopsied.
Design for Manufacturability
The single-piece design is highly complex due to the sophisticated board layout along with the concentrated location criticality of components and susceptibility to electromagnetic interference noise [EMI]. Throughout the design process, the teams tested to overcome this complexity. Working together the design engineers and the in-house manufacturing engineers and operators were able to consider all aspects of design for manufacturability. For our clients, this made working with Nortech unique because typically, the manufacturer is not as accessible during the design phase. The teams produced several prototypes before the final product design was proven and accepted. Both manufacturing and production shared feedback early in the design phase, ensuring the end product would meet the customer’s needs.
Nortech’s engineers expressed how important it was to partner with the client’s design and development team. “We need everyone’s input to make it successful.” They continued, “It’s not us and them, we’re a team.” Communication and creating deep trust were key in developing a real team that could accomplish this project. As a result, the close-working relationship with this client allowed the team to do outstanding things with the design and build of this device.
Additionally, Nortech’s Milaca facility has deep experience with higher level assemblies and integrated complex electro-mechanical devices. The team was well-prepared to meet the client’s requirements with attention to qualified materials and processes as well as regulatory requirements.
Total product lifecycle management and history, plus a flexible and robust quality management system plus having client input in each stage has made this design successful. Our client received the regulatory/agency approval necessary and in 2023 will begin marketing the newly redesigned product to medical providers worldwide.