Customizable Supply Chain Based on Customer Needs
First developed by Toyota, the practice of lean manufacturing became very popular in the 1990s and early 2000s as manufacturers around the world adopted the practice. Some benefits of lean manufacturing included reduced lead times, reduced operating costs, and improved product quality.
In our current economy the lean method has undergone a transformation to ensure everyone’s needs – from customer to supplier – are being met globally. Not only are we looking at our supply chain and how we innovate, but we are looking at the full spectrum of our services and how to deliver better fulfillment and a greater quantity of supplies. The key is to create a customizable supply chain based on customers’ needs. This means more involvement from customers, suppliers, and supplier partners to ensure alignment and focus toward one common goal. At Nortech we place safe gaps in between key stakeholders for consistency and continuity in our supply chain globally.
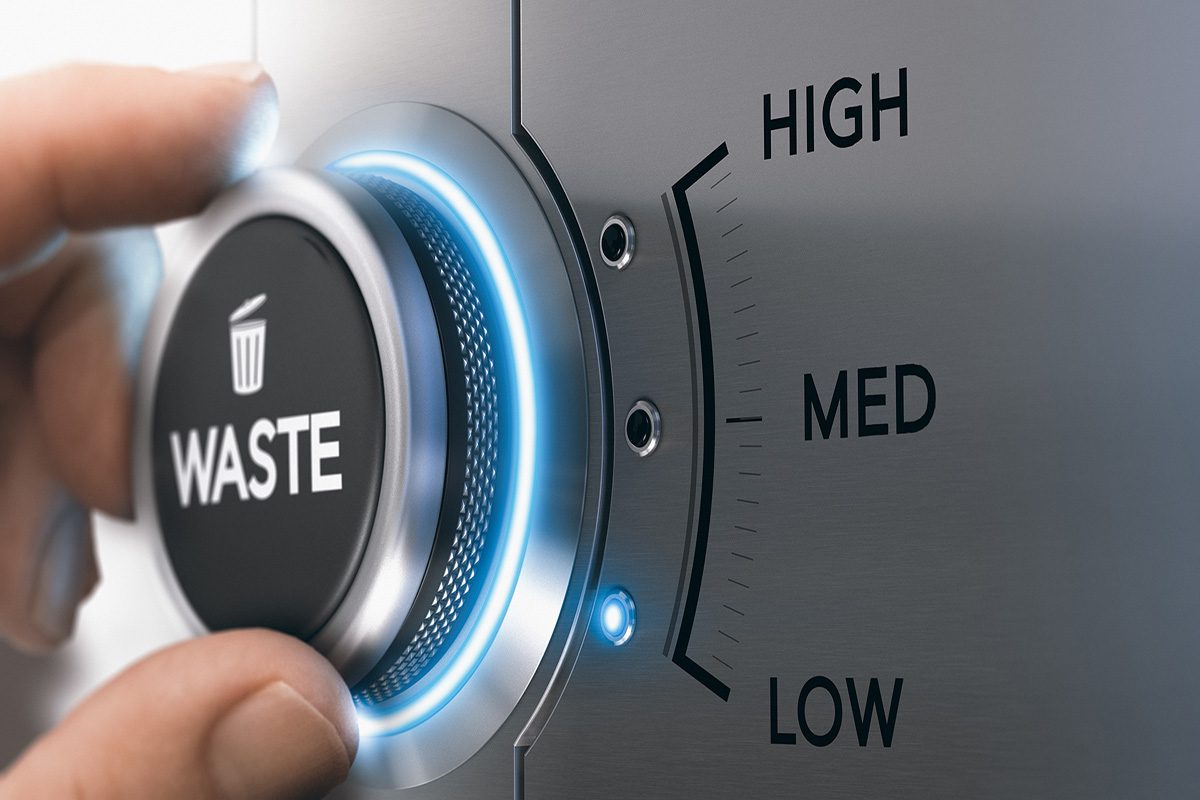
Lean Manufacturing Has Evolved
Automation has enabled efficiency and accuracy, allowing workers to focus on more value-added tasks. Notably, there has been a shift toward a customer-centric approach focused on quality, flexibility, and speed. Plus, the implementation of new technologies like big data and artificial intelligence has further facilitated the improvement of lean manufacturing processes and the identification of new opportunities for optimization. The implementation of lean practice begins with the actions which directly and indirectly create value for the customer. Nortech employees are trained in lean processes to eliminate waste from the value stream. This increases our capacity and on-time delivery.
Distilled Into Five Rotational Steps the Lean Principles Are:
- Specify the value desired by the customer.
- Identify the value stream for each product providing that value and challenge all of the wasted steps (generally nine out of ten) currently necessary to provide it.
- Make the product flow continuously through the remaining value-added steps.
- Introduce pull between all steps where continuous flow is impossible.
- Manage toward perfection so that the number of steps and the amount of time and information needed to serve customers continually falls.
Through ongoing testing, our employees learn and innovate their work for increasingly better quality and flow, less time and effort, and lower waste. Tools such as vision and sensor systems are increasingly helpful in the lean process, and multi-function cables, such as the hybrid models developed by Nortech Systems help streamline solutions with enhanced power delivery.
Lean Has a Moral Compass
Lean progresses in the context of specific situations; respect for the humanity of customers, employees, suppliers, investors, and our communities with the belief that all can and will be better off through lean practices.
By reducing anything that does not add value to a product, meaning waste, lean manufacturing seeks to increase or add product value for the customer. The seven wastes are:
- Unnecessary transportation
- Excess inventory
- Unnecessary motion of people, equipment, or machinery
- Waiting, whether it is people waiting or idle equipment
- Over-production of a product
- Over-processing or putting more time into a product than a customer needs, such as designs that require high-tech machinery for unnecessary features
- Defects, which require effort and cost for corrections
Nortech is devoted to providing exceptional value to our customers with continuous improvement and efficiency. We strive to minimize waste and maximize service without the need of coordinating multiple vendors. Our unmatched commitment to quality and timely delivery is manifested in our lean plan that encompasses cross-training for our production associates, ensuring success for every employee. We guarantee that orders will be placed and fulfilled based on our customers’ desired dates. Moreover, we are making significant progress in automating our factory floors to enhance quality for tasks that are difficult for humans due to physical constraints.