If your product development team is facing inhouse resource constraints and missing project timelines, here are three critical questions to ask:
- What are the projects that are being deferred or delayed because your engineering resources are over-allocated?
- Are inefficient design, prototyping and testing cycles leading to R&D cost overruns?
- Is your project at risk of missing the timeline or budget requirements?
Companies who engage an engineering team with deep expertise in designing for manufacturability can achieve targeted project timelines, plus design for supply chain and cost as compared to companies who design new technologies using only inhouse and contract resources.
Our client, a global cancer care technology company, was working on the development of life-changing medical device technology. Their internal development team was deployed on multiple projects simultaneously and those resource-constraints kept the team’s progress at a much slower pace than the project plan required. In addition to the design and development work, the team also faced a lengthy process to get regulatory approval on their new technology.
Design for Manufacturability, Supply Chain & Cost:
Engaging engineering design resources with deep manufacturing knowledge prior to design freeze makes prototyping cycles more efficient, lowers product development costs and improves development lead time. The team will be able to consider manufacturability, supply chain and cost during the earliest phases of design.
In order to achieve the speed to market that they desired, our client’s product development team quickly identified that early engagement with a design team strategically embedded within a manufacturing environment would provide the expertise, insight and resources necessary to achieve their product launch goals. In addition, a collaborative relationship with an engineering team with deep manufacturing knowledge would allow our client to fine-tune the design to optimize manufacturability, supply chain and cost. This strategic ‘design for manufacturability’ mindset guided the team as they developed the technology.
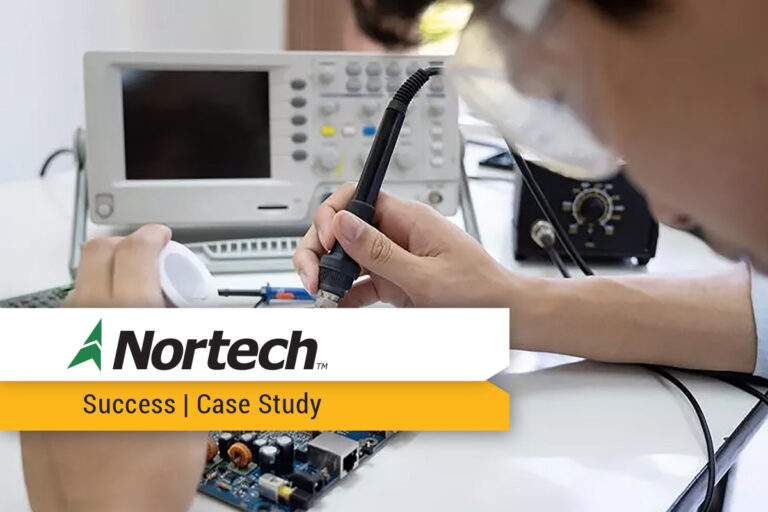
Early collaboration during the design process is crucial to achieving speed to market. In a classic study, McKinsey & Co found that a product that is six months late to market, earns 33 percent less profit over the first five years on the market. Likewise, if a new product is released on schedule, an overage in the development budget typically only impacts profits by four percent in that same first five-year window.
By partnering with Nortech and integrating our engineering designers into the team early, in the first stages of the product lifecycle, the client’s entire team had insights into the design’s manufacturability, supply chain availability and costs right from the start. This perspective allowed the team to execute the process all the way from the initial design with optimal efficiency, resulting in a product launch and regulatory approval that was both on-time and on-budget.
Results
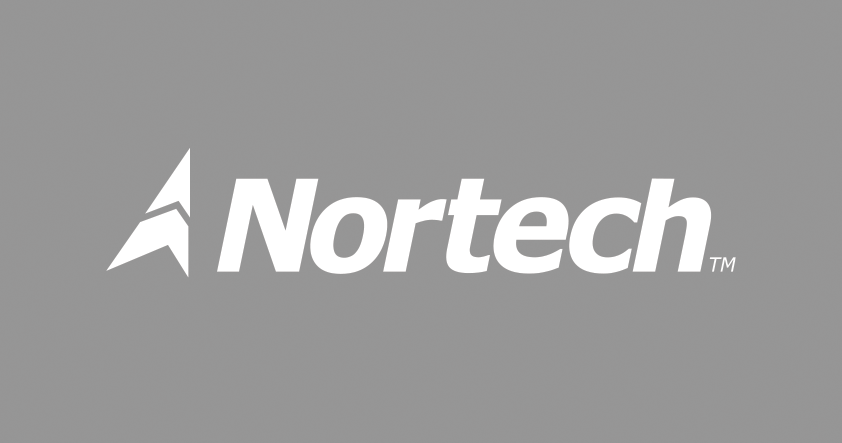
Developing new technologies in-house can be complicated and timely, even for a large global organization like our client. Our client understood that by bringing together their in-house team with Nortech’s specialized resources, that they would be able to contain costs while avoiding unnecessary cycles of design, development and prototyping.
Through this close collaboration, Nortech’s engineering team was able to build the prototypes, provide material selection, and help keep the project plan on track from the initial design through regulatory approval. Members of Nortech’s engineering team are full-time at the client’s location, and the project is currently in the verification phase on track for a timely and successful launch.
To learn more about Nortech’s program management and product launch processes, click here.