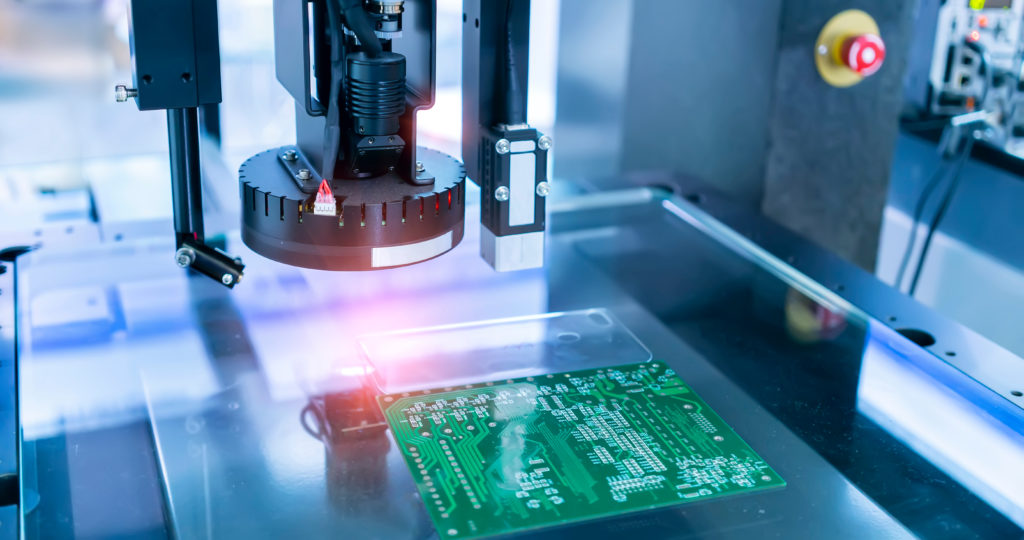
Why Is a Quality Management System so Important?
A Quality Management System (QMS) is a formal system that documents processes and responsibilities for enforcing quality policies and objectives. A QMS helps support and direct an organization’s activities to meet customer and regulatory requirements and improve its overall performance.
It covers aspects like documentation of the process, Standard Operating Procedures (SOPs), Plant Quality Guidelines (PQGs), the personnel’s completed training records, etc. It also ensures there are no gaps in the processes and that all the steps are carried out per the procedures. A robust QMS instills confidence that your product is manufactured with utmost care and quality.
What Constitutes a Good Quality Management System?
Have you heard the expression “how do you define quality” with the answer being “well, I know it when I see it?” The same sentiment can be applied to Quality Management Systems, but there are some specific elements you should consider.
Certifications
Look for certifications first. If the manufacturer is ISO 13845, AS9100, and ISO 9001 certified, you can rest assured that there is a robust QMS in place as a formal auditing process, defined by the standards body, has already done all the checking and auditing for you. These certifications guarantee that policies, procedures, and training are well defined and documented.
Written Policies, Manuals, and Procedures
Policies, procedures, work instructions, and manuals are important documents that make up a QMS. These documents guide how to complete tasks correctly and efficiently. They also establish responsibility and accountability for meeting quality objectives. Look for readily available examples of these documents when performing your assessment.
Training
Training is another critical element of a good QMS. All the written policies, manuals, and procedures in the world will not do any good if the employees are not trained in their content. Employees must be appropriately trained on the policies, procedures, and work instructions relevant to their jobs. They should also be aware of the importance of quality in the organization and how their jobs impact its overall quality performance. This training should also be well documented per certification standards as proof that this material has been presented and comprehended.
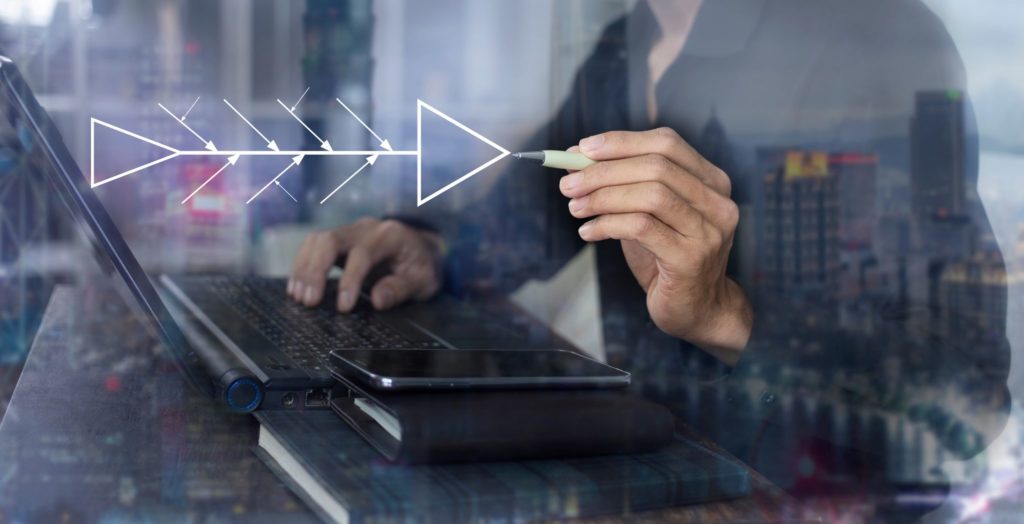
Corrective Action/Preventive Action (CAPA) Process
A QMS also includes a corrective action process for investigating and addressing non-conformities. This process helps identify the root causes of problems and puts corrective actions in place to prevent recurrences.
The steps of this process usually include an investigation that may employ tools such as the 5 Why’s, Fishbone Diagrams, or Pareto Charts to get to a root cause. Then implementation of actions to mitigate or mediate that root cause. Lastly, a solid QMS program will include a verification step roughly 30-60 days later to prove that these actions have indeed corrected and prevented the initial problem.
Defective Parts per Million (DPPM)
The metrics of a QMS can also speak volumes for assessing a contract manufacturer. For an Electronic Manufacturing Services (EMS) provider, DPPM is one way to measure the effectiveness of a QMS. This metric shows how many defects are present in a product or process. A lower DPPM means better quality and higher customer satisfaction.
Continuous Improvement
A continuous improvement process is essential for any quality management system and means that the system is constantly reviewed and updated based on feedback from customers, employees, and other stakeholders. The system should also be open to input from all team members and evaluated as part of a site-wide improvement effort.
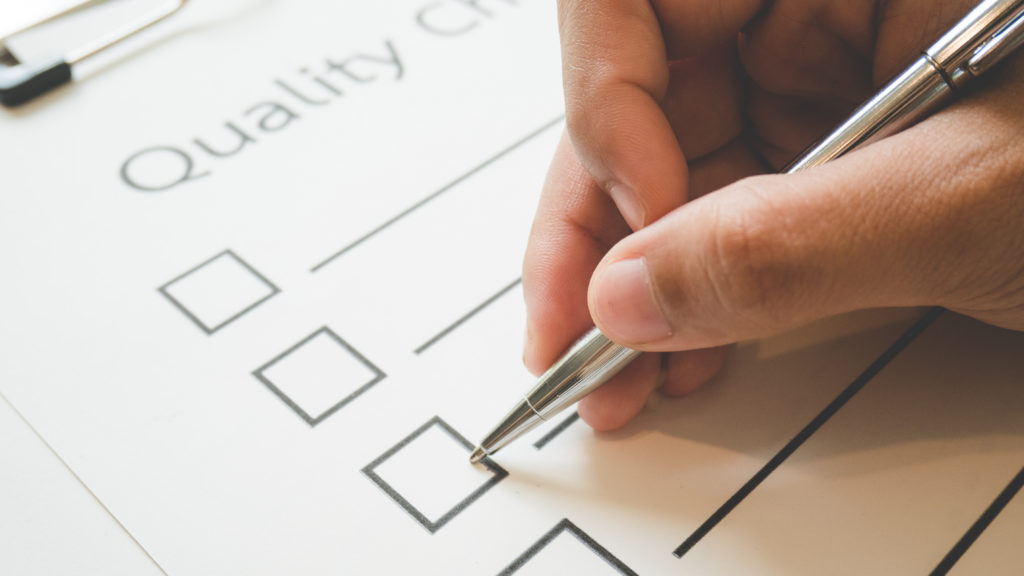
Other Factors of a Good Quality Management System Assessment
When conducting a QMS Assessment, there are several other factors to consider when determining if you can work with a contract manufacturer successfully.
Document Transfer
Most certifications require documentation of procedures and policies. However, documentation of designs, customer-required documents, and results are also a must-have for a good working relationship. A robust certified QMS system will likely have all the necessary documents defined and available for a seasoned customer. A flexible QMS can create and transfer those same documents to any customer, per their quality protocols, regardless of the maturity of the customer’s quality system.
Filling the Gaps
Selecting a supplier with an excellent QMS is one way to fill the gaps in an existing quality system. If training and internal audits are not currently meeting requirements, finding a contract manufacturer with those systems in place can solve that problem. If you are missing a certification, such as ISO 13485 for medical devices or AS9100 for aerospace and defense products, selecting a contract manufacturer with those certifications is a solution.
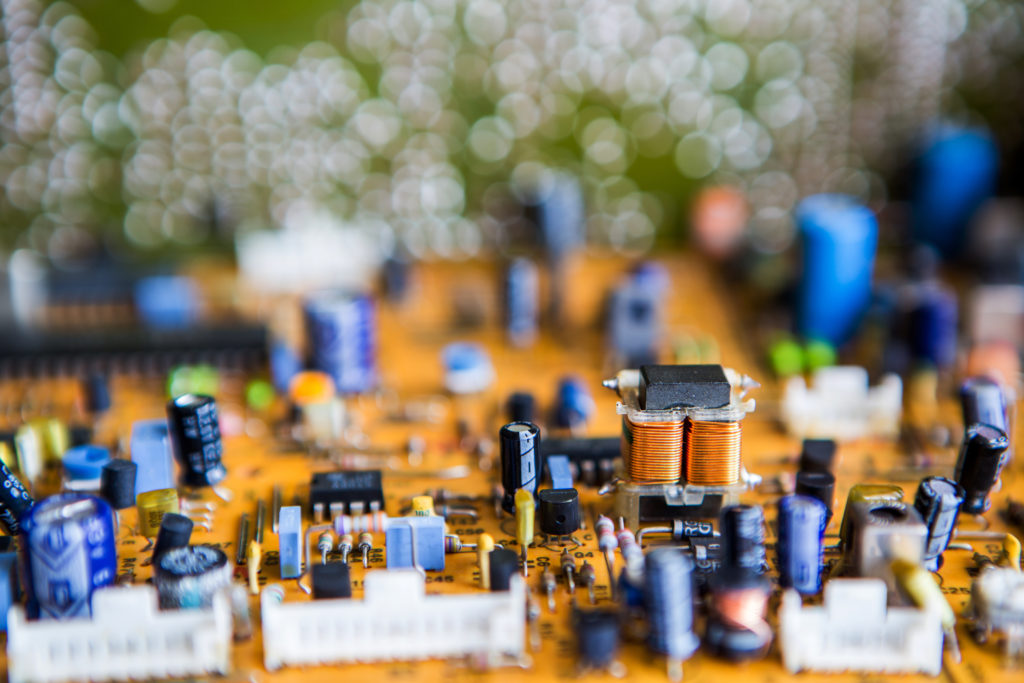
Supplier Management
Supplier management is a critical part of the manufacturing process. It ensures that parts and materials meet quality standards and prevents production delays and disruptions.
Contract manufacturers have the experience and expertise already in place to select and manage suppliers effectively and the resources to perform regular audits, implement supplier corrective actions (SCARs), monitor DPPM, measure on-time deliveries, and create supplier scorecards to summarize all of these activities.
Consider that a single cable assembly could involve 20 or more suppliers, or a printed circuit board assembly typically involves up to 100 or more suppliers. Letting the contract manufacturer handle supplier management can help improve the manufacturing process’s quality, prevent production disruptions, and save you time and resources.
Select the Best Manufacturer
When it comes to engineering and manufacturing, there is no one-size-fits-all solution. The contract manufacturer you select should be based on your specific needs and product requirements.
You should consider their engineering capabilities, design and prototyping services, test and validation capabilities, supply chain management, and quality management system. By doing your research upfront, you can ensure that you select the best contract manufacturer for your project and avoid costly mistakes down the road.
Nortech Systems has a long history of successfully working with customers at all development levels – from startups to long-standing, mature product manufacturers – our systems are robust enough to have what you need while flexible enough to adapt to your wants. Contact us to help you reach your product development and production goals.