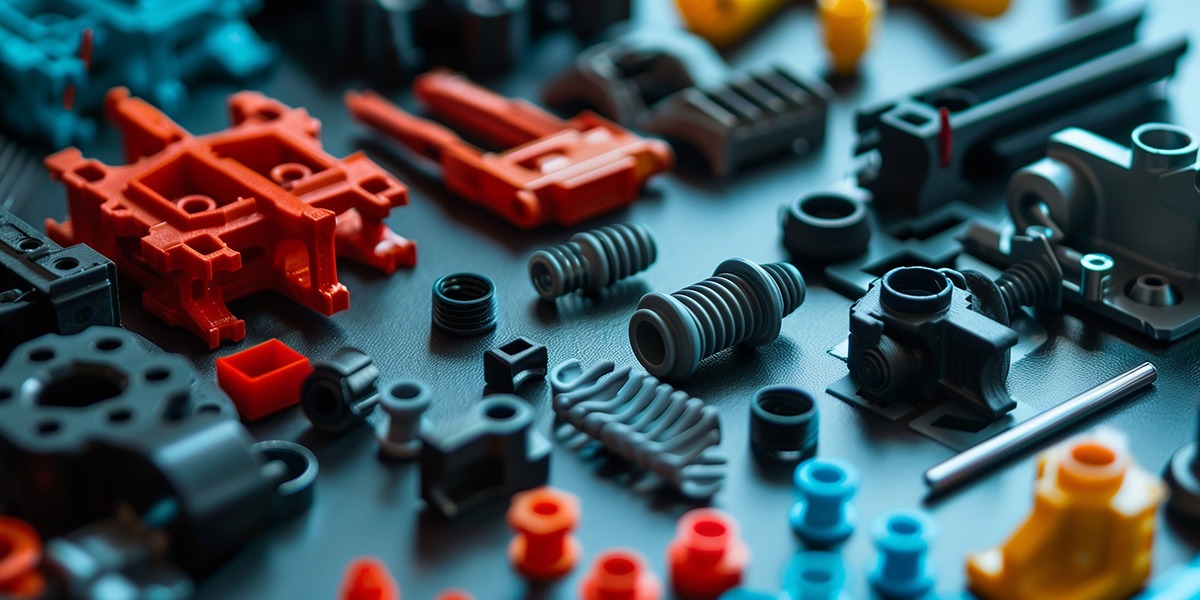
In an era where speed, efficiency, and innovation are paramount, the ability to design and manufacture mold tooling in-house is a game-changer for engineers at Nortech and industries worldwide. By harnessing the power of 3D printed prototypes and advanced machining technologies, manufacturers like Nortech can achieve unprecedented control over their production processes.
Faster Lead Times
Traditional mold tooling methods often involve extensive machining processes, which can result in lead times stretching into weeks or even months. This delay can be a significant bottleneck, especially in fast-paced industries where time-to-market is crucial.
3D printing revolutionizes this scenario by enabling rapid prototyping and faster production of low-volume or complex molds. The ability to quickly produce high-quality molds in-house not only accelerates the development cycle but also allows companies to respond swiftly to market demands, thus gaining a competitive edge.
Reduced Costs
Outsourcing mold tooling can be a costly affair, involving multiple external vendors and logistical complexities. In-house manufacturing eliminates these dependencies, significantly reducing overall costs.
Moreover, 3D printed prototypes typically requires less material compared to traditional machining methods. This material efficiency not only translates to cost savings but also aligns with sustainable manufacturing practices by minimizing waste.
Enhanced Design Flexibility
One of the most compelling advantages of 3D printing is its ability to overcome the limitations of traditional machining. Complex geometries, internal channels, and intricate features once considered unachievable are now within reach. The world of mold tooling is no longer a binary choice between 3D printing and traditional machining.
This enhanced design flexibility unlocks innovative mold designs to improve part quality but also boost production efficiency. Manufacturers can experiment with novel concepts and refine designs without the constraints imposed by conventional methods.
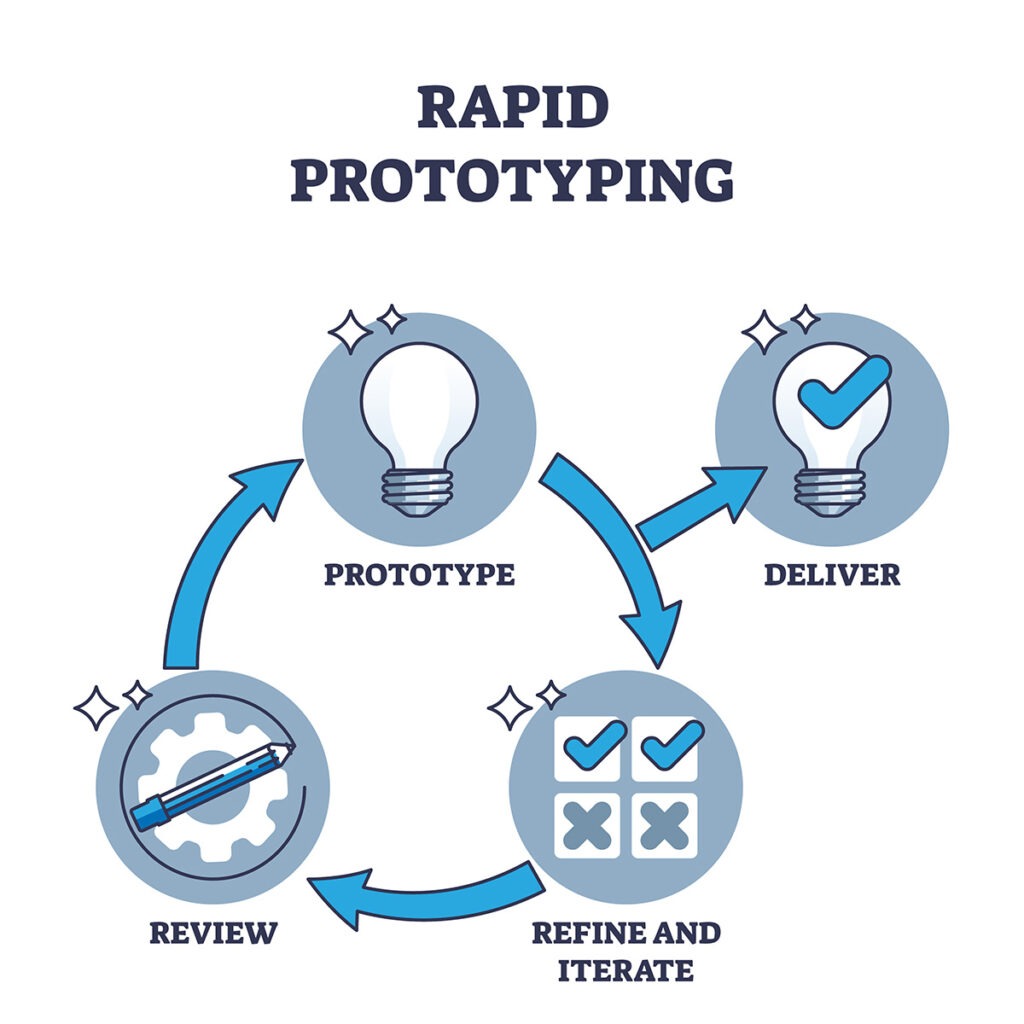
Greater Control & Iteration
In-house mold tooling empowers manufacturers with greater control over their production processes. The ability to iterate on designs quickly and efficiently enables rapid testing and refinement of mold features.
At Nortech we specialize in low volume production for our clients because we value quality in our process. Utilizing 3D printers help our engineers quickly iterate designs by allowing for greater control on how to create fixturing and the layout. This iterative approach leads to optimized production processes, reducing the likelihood of errors and enhancing overall product quality. Our engineers also experiment with varied materials and techniques, ensuring the final product meets the highest standards.
Iterative Design in Aerospace Components
In the aerospace industry, precision and reliability are non-negotiable. By adopting in-house 3D printing for mold tooling, aerospace manufacturers like Nortech, can rapidly iterate on component designs, conducting rigorous tests and refinements. This process ensures the final components not only meet but exceed stringent industry standards. In-house mold tooling, eased by 3D printing and advanced machining technologies, is revolutionizing the manufacturing landscape. The benefits—faster lead times, reduced costs, enhanced design flexibility, and greater control—are driving industries toward more efficient, innovative, and sustainable production processes. For 3D printing enthusiasts and electronic manufacturing customers, embracing in-house mold tooling is not just an option; it’s a strategic move for the future. By investing in this cutting-edge approach, businesses can unlock new levels of efficiency and innovation, positioning themselves as leaders in their respective fields.
Nortech’s In House Molded cable construction offers many advantages including water-resistance, abrasion protection and maximum strain relief effectiveness. Flex-induced stress on wires, connector and contacts is reduced. The molding process provides excellent electrical insulation properties, less exposed metal than mechanical back-shells and the cable can enter the connector from any angle. Nortech can cast mold urethanes, silicones, and epoxies. We can transfer mold elastomers such as Neoprene and VITON®. Injection molding of thermoplastics such as polyurethane, PVC and nylons, meet any molding requirement you may encounter. We recognize the importance of reliable and sensible molded cable designs at Nortech and know how valuable our customers find holding a physical representative of their product in their hands. Our commitment is to ensure our client’s products maintain peak performance and meet all their requirements.
With in-house molding and 3D printed prototypes from Nortech, you can trust in their durability against cold temperatures and aging – reducing replacement needs and costs. These sealed-for-life assemblies not only save you time but also money in the long run.