One of the key strategies to a successful on time and on budget product introduction is to partner with a firm that offers high-value program management services.
As you evaluate possible partners, consider the project management methodology as well as the frequency and completeness of the communication with your team. Nortech’s program management team focuses on delivering consistent results by breaking down a project into five coordinated phases to make sure everything stays on track. These phases are customized to meet client requirements as well. Regular check-ins and frequent communication with our clients provides status updates on accomplishments, issues, risks, costs, and timelines.
Nortech’s program management process is flexible and customizable. Depending on your budget and resources, we can make adjustments to meet your end goal. Custom project schedules to track deliverables, financials and responsibilities are customized to meet each client’s project needs. Our customizable process allows us to work with any size company and our project phases break down everything you need to align with FDA regulations, helping your product go to market with regulatory approval.
As an integrated service provider of engineering, design, fulfillment, and manufacturing, we pull numerous resources into your project as needed. This allows you to transfer the headache of managing multiple suppliers from your team to ours. Our integrated manufacturing and engineering services offer a quicker speed-to-market strategy, reducing transportation costs and time, allowing for better quality control, giving more flexibility in product design, and providing seamless transitions between design, manufacturing, and market release.
By breaking down your project into phases we can focus on each part with experienced professionals making sure every critical step is completed. Here is a high-level overview of those 5 phases:
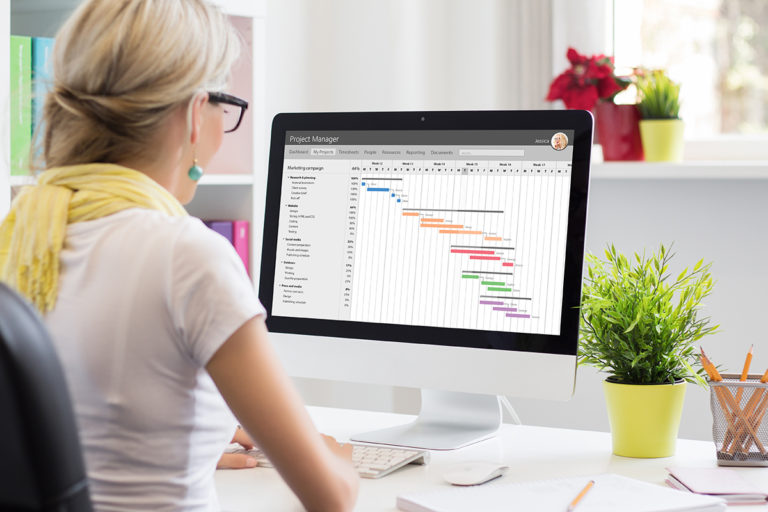
Phase I Concept Development
This phase is intended to define the clinical/marketing input, design feasibility, and user needs.
Includes documentation and proof of concept prototype. Involves reviewing user/customer or marketing requirements that are used to develop concepts and models in evaluating the concepts and models for feasibility, technology evaluation an IP review and a regulatory analysis.
Phase II Planning And Architecture
In Phase II a project plan defining the customer requirements is created. A risk analysis is conducted, and technical regulatory requirements are determined. A requirements document is finalized.
Deliverables included are a detailed project plan, risk management plan/clinical hazard analysis, product/system requirement specifications, regulatory requirements checklist and design review minutes.
- Detailed project plan describes the customer requirements for the project. Project tasks, resources, deliverables, responsibilities and milestones that are combined to create an overall project plan. The project plan must include a detailed schedule, manufacturing strategy, clinical plan, regulatory plan and quality Plan review. The plan should provide a framework for effective management of risks associated with the use of medical devices per ISO 14971. This plan specifies the process by which the project team can identify hazards associated with a medical device and its accessories, estimate and evaluate the risks associated with those hazards, control those risks and monitor the effectiveness of that control.
- The Requirements Specifications should define the functional, physical, reliability, safety, packaging and labeling specifications for the device/system.
- A design input checklist showing all the essential requirements for the device, and the harmonized/consensus standards required to demonstrate compliance.
- Design reviews are conducted as a comprehensive and systematic examination of a design to evaluate the adequacy of the design output requirements, to evaluate the capability of the design to meet these requirements and to identify problems.
Phase III Detailed Design Development
In Phase III, the design inputs are used to develop design outputs. These design output deliverables are initially released and become the basis of the Device Master Record (DMR).
Deliverables included are design documentation, manufacturing documentation, material procurement, regulatory documentation, verification documentation, design review documentation, marketing documentation and configuration management.
- Device design documents needed are design Outputs. They typically include assembly drawings, schematics, and software source code.
- Manufacturing documentation needed are supplier approval, router (including sequential lists of all processing operations), manufacturing work instructions, manufacturing test fixture test and any burn in fixtures, training, process validation plan and cost of goods analysis.
- Material procurement needed are acquired materials and prototype build.
- Regulatory documentation needed includes a clinical/ regulatory plan which is a clinical protocol and roll out plan, number or units, and worldwide regulatory submission plans, including rational.
- Verification documentation requires Failure Modes and Effects Analysis (FMEA) risk analysis, verification planning (design and reliability testing actives), and design analyst testing.
- Design review documentation needed are design reviews which are conducted as a comprehensive and systematic examinations of a design to evaluate the adequacy of the design output requirements, the capability of the design to meet these requirements and to identify problems.
- Marketing documentation needed are labeling and literature planning to determine what product support documentation used by the customer or used in the sale to a customer.
- Configuration management (DMR) which is a compilation of all information needed to build a product.
Phase IV Test Verification& Optimization Documentation
In phase IV, design verification takes place. The Design outputs created in Phase III are evaluated for conformity against the design inputs created in phase II. A pre-production build is performed so that product is available for verification tests. At the conclusion of verification, all documentation in the BOM is moved to production control. This process entails the “transfer” of the product from design to production.
Deliverables included are design documentation, manufacturing documentation, material procurement, regulatory documentation, verification documentation, design review documentation, marketing documentation and configuration management.
- Design documentation include design changes to design input and output specifications.
- Manufacturing documentation needed include, Process documentation, process FMEA, Process validation protocol and equipment installation qualification, Process and equipment validation reports, Production qualification plan. Approved vendor list, Cost of Goods sold analysis.
Acquire materials and pre-production build. - Design review
- Verification testing and reports (design and reliability testing activities are created).
- Design review documentation needed are animal evaluation and regulatory submission (preparation and submission of the required documentation for clinicals in the European Union, the Design Dossier for CE Marking, and the required documentation for the FDA).
- Marketing documentation needed are labeling and literature, customer training plan and customer service plan to identify the intended customer service methodology.
- Corrective action status, a list of all associated product corrective actions opened and closed during the phase, and DMR release.
Phase V Validation & Launch
In Phase V, a production build for clinical trials is performed and human clinical trials conducted. After a final clinical report and risk analysis report are completed, regulatory approvals are obtained, and a market release plan is utilized.
Deliverables included are material acquisition, design documentation, manufacturing documentation, regulatory/ clinical documentation and reliability documentation.
- Production qualification builds, the acquisition and/or build of “verified and validated” product that are for human use.
- Design documentation needed are patents analysis, system validation report and final trace matrix.
- Manufacturing documentation include, Costed BOM analysis (updated breakdown of estimated product).
- Reliability documentation include, regulatory approvals, labeling and literature, clinical evaluation/report, market release plan, risk management report, corrective action status and project close out audit.
At Nortech we value relationships with our customers and communication. That is why we work with you at every point throughout the process. Our five phases help breakdown the process for you providing structure for project delivery. It allows us to ensure that deliverables produced in each phase are meeting their purpose preparing us to move onto the next phase. Our project process allows us to develop your product visions in the shortest amount and time and for the lowest cost.
Our team features some of the most experienced and creative minds in the industry. Armed with the best practices and the right tools, we can help you optimize your project design to exceed expectations. Contact us today to get started.